Sterility Testing: A Comprehensive Guide

What is Sterility Testing?
Sterility testing is a microbiological examination method used to determine whether a product that is required to be sterile has been contaminated by microorganisms. It is commonly applied in the pharmaceutical, biotechnology, and medical device manufacturing industries.
WATCH NOW: Understand Sterility Testing in 3 minutes!
The Purpose of Sterility Testing
Sterility testing is applicable to most pharmaceutical products mandated to be sterile, including injectable drugs, eye drops, solid pharmaceuticals, and various sterile medical devices. Its scope of application is broad.
If these products are contaminated with microorganisms, they may reduce efficacy or even cause infections and other severe complications upon contact with the human body. Therefore, the primary goal of sterility testing is to ensure that products designated as sterile, after undergoing aseptic manufacturing or terminal sterilization processes, are free of viable microorganisms, ensuring safety and effectiveness in clinical use.
Definition of Sterility and International Standard
Definition of Sterility
Sterility refers to the absence of viable microorganisms in a sample, which is a fundamental requirement for ensuring the safety of pharmaceutical products. The internationally recognized benchmark for sterilization efficacy is the Sterility Assurance Level (SAL). A product is considered sterile if SAL ≤ 10⁻⁶, meaning the probability of microbial contamination is less than or equal to one in a million.
International Standards for Sterility Testing
Standards such as ISO 11737-2, USP <71>, EP, JP, and the Chinese Pharmacopeia define the requirements for sterility testing, including test environments, sample preparation, and operating procedures. These ensure compliance with global standards and provide reliability for test results.
How is Sterility Testing Performed?
Two commonly used methods for sterility testing are the Membrane Filtration Method and the Direct Inoculation Method. According to the Pharmaceutical Inspection Co-operation Scheme (PIC/S), both methods must be performed under aseptic conditions in a Grade A cleanroom within a Grade B environment. The choice of method depends on the sample characteristics.
Method 1: Membrane Filtration Method
This is one of the most widely used sterility testing methods, suitable for liquid samples, solid samples, and medical devices with pipelines that can be rinsed and filtered.
Principle: The sample is filtered through a membrane with a pore size of less than 0.45 µm to capture potential microorganisms. The membrane is then transferred to an appropriate culture medium for incubation to detect the presence of viable microorganisms.
Equipment for Membrane Filtration Method
The required equipment includes vacuum pumps, filtration manifolds, and membrane filters. Reusable stainless-steel filter cups can be autoclaved or flame sterilized with a Lab burner to save sterilization time.
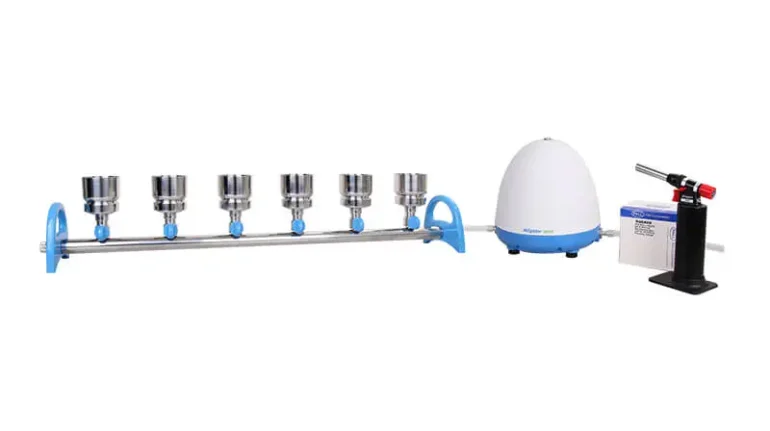
- Save time & space
- Quick-assembly and disassembly
- Innovative vent valve design
- Offers 3-port and 6-port options

- Innovative rotary design
- Individual control valve
- Durable and autoclavable
- Offers 6-port and 12-port options
Operating Steps for Membrane Filtration Method
The operational process of the membrane filtration method for sterility testing can generally be divided into four stages: sample pre-treatment, sample filtration, membrane incubation, and result interpretation. The following will provide an explanation of each stage in sequence.
1.Sample Pre-treatment: Depending on sample type, pre-treatment is required before filtration to improve flow rate or prepare the sample for filtration.
Sample Type | Filterable Liquids | Ointments and Oils | Solid Antibiotics | Medical Devices |
Pre-Treatment Method | Dilute with sterile liquid if too viscous. | Dissolve in isopropyl myristate, heat if necessary (up to 44°C). | Dissolve in sterile solution. | Rinse with sterile solution and filter the rinsate. |
2.Sample Filtration: Pour the pre-treated sample into the filter funnels. Use a vacuum pump to create negative pressure, enabling vacuum filtration. For larger quantities, multi-branch filtration manifolds can be used.
3.Membrane Incubation: Transfer the membrane to a culture medium using sterile tweezers, seal, and incubate at an appropriate temperature for 14+ days.
4.Result Interpretation: Observe the culture medium for microbial growth. If no changes occur, the sample is sterile and complies with sterility testing requirements. If the medium becomes turbid, it indicates the presence of viable microorganisms, meaning the sample does not meet sterility requirements.
Method 2: Direct Inoculation Method
Direct Inoculation Method is designed for samples that cannot be processed using membrane filtration, such as insoluble solids or medical devices that are unsuitable for filtration.
The principle involves directly placing the sample into a culture medium and monitoring for microbial growth to assess sterility.
Operating Steps for Direct Inoculation Method
The operational process of the direct inoculation method can generally be divided into three stages: Sample preparation, culture medium incubation, and result interpretation. The following provides an explanation of each stage in sequence.
1.Sample Preparation:After preparing the sample, place it into the culture medium.
Sample Type | Solid Samples | Liquid Samples | Medical Devices |
Preparation Methods | Use an appropriate solvent to prepare a suspension, ensuring the sample can evenly contact the culture medium. | Directly add an appropriate amount to the culture medium for incubation. | Immerse the entire device or a suitable part of it directly in the culture medium, ensuring all surfaces that may come into contact with microorganisms are fully covered by the culture medium. |
2.Culture medium incubation: Seal the culture medium and incubate for 14+ days.
3.Result Interpretation: Observe the culture medium for turbidity to determine sterility. If no changes occur, the sample is sterile and complies with sterility testing requirements. If the medium becomes turbid, it indicates the presence of viable microorganisms, meaning the sample does not meet sterility requirements.
Comparison of Methods: Membrane Filtration and Direct Inoculation
The choice between the Membrane Filtration and Direct Inoculation methods depends on sample characteristics to ensure accuracy and reliability.
Sterility Testing | Membrane Filtration Method | Direct Inoculation Method |
---|---|---|
Applicable Samples | Liquid samples, soluble samples, medical devices with tubing | Samples unsuitable for membrane filtration, such as high-viscosity solutions or specialized medical devices |
Operating Principle | Uses a membrane with pore size ≤0.45 μm to capture microorganisms, followed by membrane incubation | Directly cultures the sample in a medium and observes for microbial growth |
Required Equipment | Membranes, vacuum pump, manifold filtration system, stainless steel filter holder, sterilization equipment (e.g., flame sterilization with a bunsen burner or autoclaving) | Culture medium, sterile containers |
Incubation Days | 14 days or more | 14 days or more |
Appendix: Choosing Vacuum Filtration Equipment for Membrane Filtration
Reliable equipment is crucial for membrane filtration. A vacuum filtration system, including vacuum pumps, manifolds, and sterilization tools, offers efficient and economical filtration.
Contact us to find the perfect vacuum filtration system tailored to your needs!
Recommended Vacuum Filtration Equipment
| Vacuum Pump | Vacuum Manifold | Rotary Vacuum Manifold | Flame Sterilizer |
SolarVac 601 – MB Rotary Multi-Branch Manifold | Dragon 100 | |||
| ||||
Rocker 300 |
ROCKER’s vacuum filtration systems reduce contamination risk and improve lab efficiency, making them the ideal choice for sterility testing.